SCHEDULE
The span of this JCATI Carbon Fiber Recycler project is one academic year – three 10-week quarters with a deadline in the first week of June. The project’s design process was limited to fall quarter consisting of Report/Proposal Writing, Analysis, and Documentation. The Gantt chart includes estimated and actual timeframes for each task. There are several tasks that took longer than expected to complete. Some examples include tasks 1a, 2a, and 3a taking twice as long as anticipated to finish. These tasks took longer due to the need for background research to be collected and design ideas to be formed beforehand. It is important to completely understand the problem and all design requirements/constraints in order to redesign a functional, working oven heating system. After the solution was determined and the first analyses and drawings were made, the remaining tasks were less time consuming.
Winter quarter included the purchasing of all parts and materials as well as the construction of the Recycler. One part purchased was the clamping u-bolts that will be used to mount each heater on the side-walls. One component to be assembled is the back panel to the electrical enclosure.

Figure 1: Gantt chart
Construction
In January, many design changes were made. Additionally, further analysis and study needed to be made on the electrical schematics specifically. Figure 1e shows more time was spent on drawings as new sub-assemblies were decided to be created. To be more specific, the Oven Enclosure, Oven Door, and Electrical Enclosure were divided into multiple parts and were made into sub-assemblies. This required more time to be spent modelling drawings, planning the manufacturing process, and assembling all parts. Therefore, the project started extremely behind schedule which posed a huge risk to the completion of the project’s construction. To combat this issue, most of the manufacturing had to be done in February.
Testing
In spring, the entire system should be completely assembled. This quarter will consist of testing and redesigning the oven heating system. Testing parameters will be listed and the results will be delivered via website presentation. The schedule for spring is displayed in sections 6 and 7 as Device Evaluation and Deliverables in Appendix E. This portion of the project focused on the procedural preparation, conduction, and analysis of three tests. In addition, a large amount of time was catered to wrapping up the project and getting it ready for presentations at the JCATI Symposium in April and SOURCE, the Symposium of University Research and Creative Expression, in May. Due to these tight timelines, the device testing had to be conducted early in the term. Tests 1 and 2, in Appendix G1 and G2, were conducted in time for both events. However, the last test was delayed a few weeks because it required shredded carbon fiber material in the oven, which was not ready yet. Therefore, after part delivery and final assembly of the shredder, more material was able to be produced for the oven and testing was able to resume. This allowed all testing to be done prior to the end of the term.
BUDGET
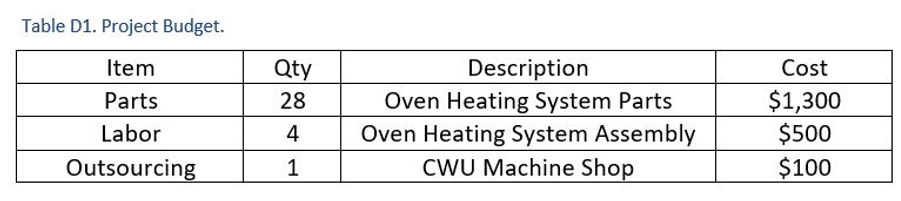
The parts that were more costly to this Oven Heating System are the forced convection fan, latch, and insulation materials. The less costly parts include the smaller components to each assembly such as the clamping U-bolts for the cartridge heaters and hose fittings for the argon tank. Many budget changes have occurred in winter quarter that were not forecasted last term due to new design changes. Although the previous estimated budget for all parts were $800, a total of $1,050 had actually been spent on purchased parts. The more expensive parts ended up being a new, bigger enclosure for the back panel to hold all electrical components, the door latch, and mineral wool insulation. While the testing phase incurred some minor smoking issues, there was no need to purchase more insulation since it was purchased in bulk during winter quarter. Since there was plenty of extra insulation material, the leakage problem was able to be resolved in a quick manner. For the project in the future, there is enough extra insulation if it is decided to increase the oven dimensions to help decrease the outer surface temperature back down to a safe value.
​
Processes that needed to be outsourced involved machining the oven enclosure to hold the heating system parts. The oven needed holes/ports for clamping U-bolts, the convection fan and motor, and hose fittings. The CWU Machine Shop was the outsourcing location of choice. In addition to machining the oven, all wires needed to be connected and fastened correctly to construct the back panel that holds all electrical components properly. Since this is the only manufacturing that will need to be done outside the oven enclosure, most manufacturing still took place within the oven.
​
Most of the labor involved in this project was assembly. The goal was to minimize machining efforts and to order parts that follow standard sizes. Therefore, the labor costs was estimated to be $1,000. Due to the increase in purchased parts, this was expected to minimize total machining efforts. Therefore, the estimated labor costs for this project have been reduced to $500.
​
The total project cost is $1,900. Part costs are around $800, Labor costs are $1,000, and Outsourcing is about $100. Since the total budget estimate is $1,900, this still does not exceed that baseline. However, the estimated cost for parts have been updated to $1,300 while the labor costs have been reduced to $500. The cost of this project is supported by the Joint Center for Innovation Technology (JCATI).